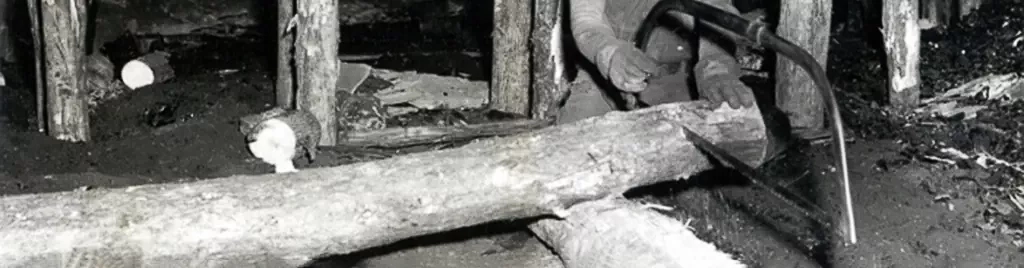
Posted May 3rd, 2022
What is Roof Bolting?
Roof bolting is a method of roof and ground support in potash, trona, coal, and hard rock mines. Introduced in the late 1800’s and rising to prominence in North America throughout the 1940’s and 1950’s, roof bolting sought to combat risk of roof fall injuries and fatalities in the underground mine and has since become a standard support method in mines worldwide. The roof bolting process and the equipment that facilitates it have constantly been evolving to improve the productivity and, most importantly, the safety of the underground mine.
Before Roof Bolting
Prior to widespread use of roof bolting, many mines relied on wooden beams to support the roof. A mine worker would form mounting holes in the floor, cut the beams to size, and position them upright throughout the mine. While it was seen as an adequate solution at the time, wooden supports came with some major disadvantages:
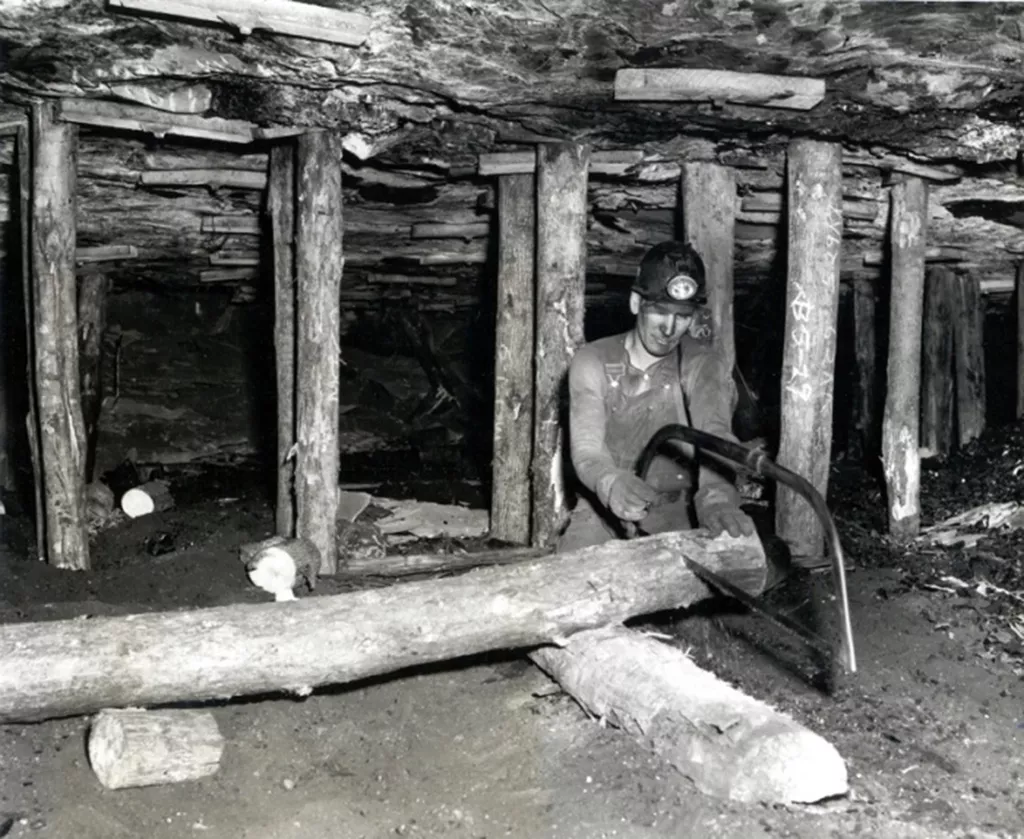
Photo courtesy of Mining USA.
One of the most significant shortcomings of wooden roof supports is that they are reactive and not proactive. This type of passive support does little to actively increase the strength of the roof. Rather, wooden roof supports try to prevent the roof from collapsing when it inevitably weakens or fails. An active support method, like roof bolting, works to prevent the failure from occurring entirely.
The Process of Roof Bolting
Before operators can begin positioning roof bolts throughout a mine, safety-minded experts must first consider the unique geological characteristics of the mine, along with the type of underground mining being performed and the anticipated stresses formed during said mining. From there, these experts develop a roof bolting practice best suited for their application. Among common roof bolting practices are suspension bolting, arch building, and beam building.
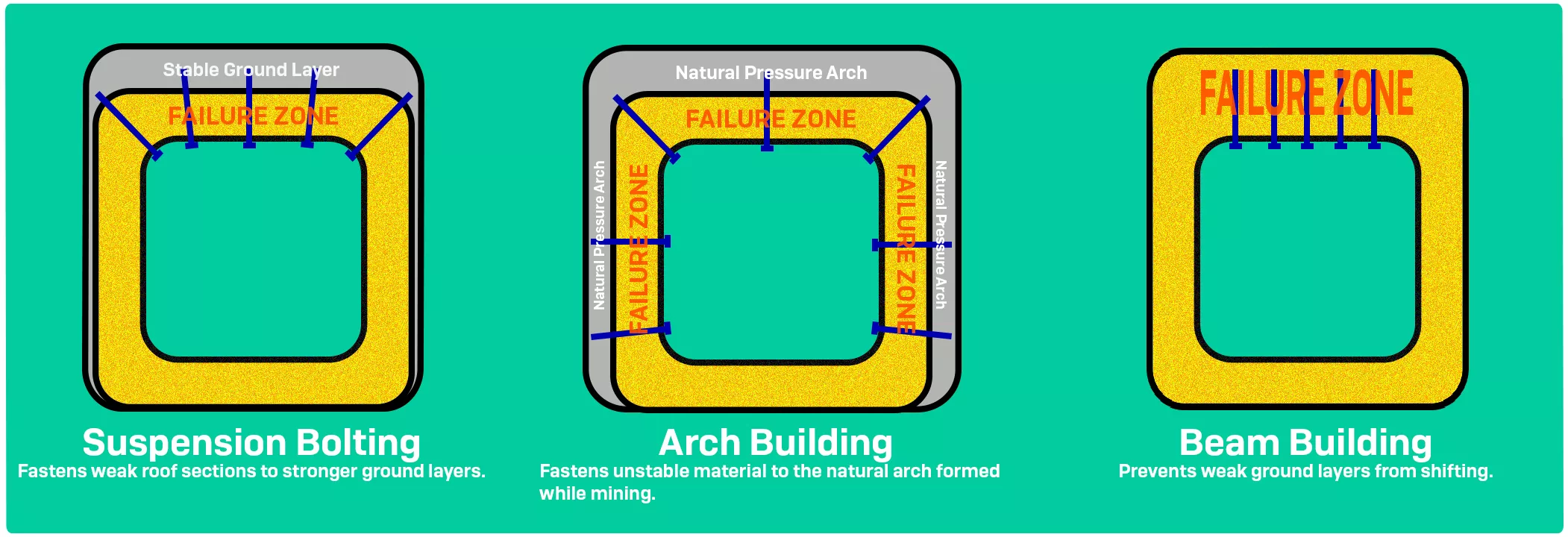
To install roof bolts, a mine may equip a crew of workers with handheld roof bolting machinery, employ a fleet of Standalone Roof Bolter Tractors or, if they have unique spatial restrictions, may opt for roof bolting attachments mounted to other pieces of mining equipment. As is the case with choosing the method of roof bolting, the equipment a mine uses depends on what is most appropriate for the geological conditions of the mine and for the safety of its workers.
A Matter of Safety and Productivity
Since its introduction over a century ago, roof bolting has become a standard method of roof support in underground mines worldwide. Compared to passive roof support methods, such as wooden support beams, roof bolting provides a safer environment for mine workers and offers better access for high-quantity production equipment.
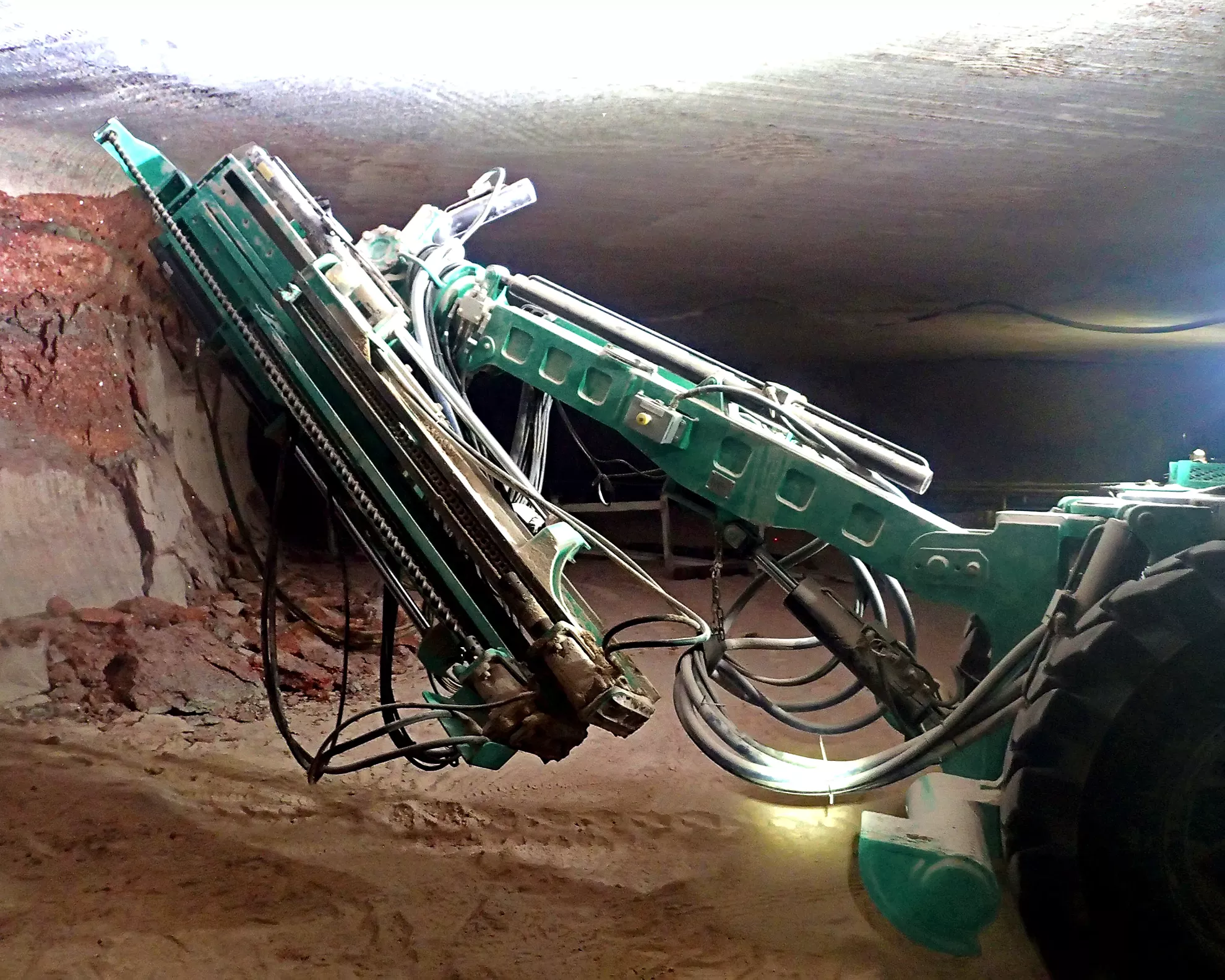
A Prairie Machine Xcel Roof Bolter underground in a potash mine.