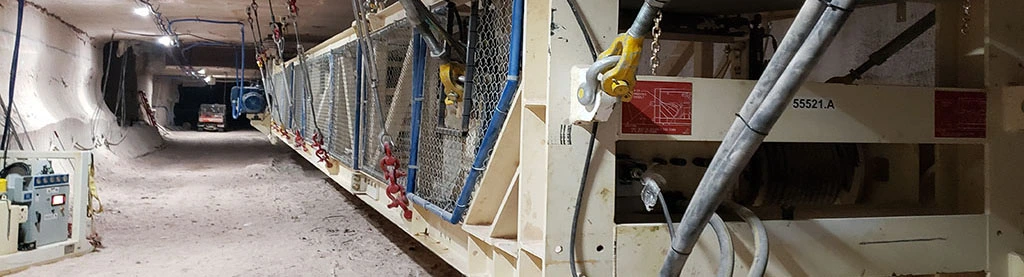
AUXILIARY MINING EQUIPMENT
Prairie Machine's line of Auxiliary Mining Equipment offers customized, cost-effective solutions to the meet the needs of an individual mining operation. The Auxiliary Mining Equipment line is designed to integrate into a site's already-established machine infrastructure or to be used in conjunction with Prairie Machine's Continuous Boring and Continuous Haulage lines to ensure a safe and productive mine site.
ROCK SUPPORT EQUIPMENT
XCEL CAROUSEL BOLTER
The Xcel Carousel Bolter expedites large scale rock reinforcement, ensurining minimal downtime during mining operations.
The Xcel Carousel Bolter is mounted to an Xcel Continuous Boring Miner to facilitate mining and rock support operations without the need for a standalone piece of rock support equipment. A drill steel, eight roof bolts, and eight associated resin tubes are all housed within the onboard carousel to ensure that support bolts are installed as efficiently and as securely as possible.
The Xcel Carousel Bolter decreases site downtime by supporting the roof above the Continuous Boring Miner as it advances. Any shuttle car operators or any other personnel working behind the Continuous Boring Miner can then proceed safely without waiting for a standalone piece of equipment to support the working area.
Using the standard wireless remote control, Xcel Carousel Bolter operators can install all eight roof bolts and resin tubes while maintaining a safe distance and machine safety interlocks ensure that operators are protected while manually interacting with the carousel.
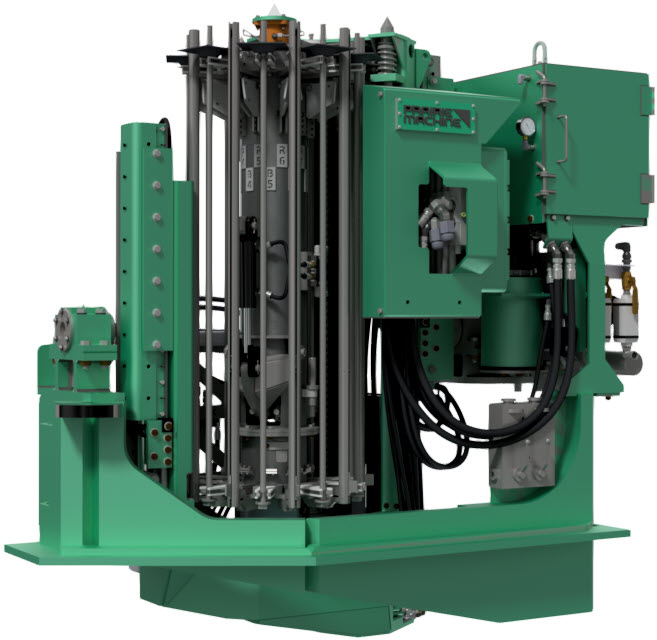
Series | Standard |
---|---|
Carousel Capacity | 1 Drill Steel 8 Roof Bolts 8 Resin Tubes |
Bolt Length | 5.25 ft |
Bolt Length | 1.60 m |
Weight | 4,650 lbs |
Weight | 2,110 kg |
XCEL ROOF BOLTER
The Xcel Roof Bolter ensures that soft rock mines can continue production safely and effectively.
Available as a standalone tractor unit or as an integrated component on an Xcel Continuous Boring Miner or Rokion Battery Powered Truck, the Xcel Roof Bolter is custom-engineered to meet a mine site's unique roof stability needs.
The Xcel Roof Bolter Tractor conforms to Tier 4 diesel engine standards, with onboard exhaust treatment systems in place to keep the air within the mine site as clean as possible. Standard safety systems, including a fire suppression system and falling object protective structure, allow the operator to confidently secure the roof and allow additional equipment and personnel to safely enter the area.
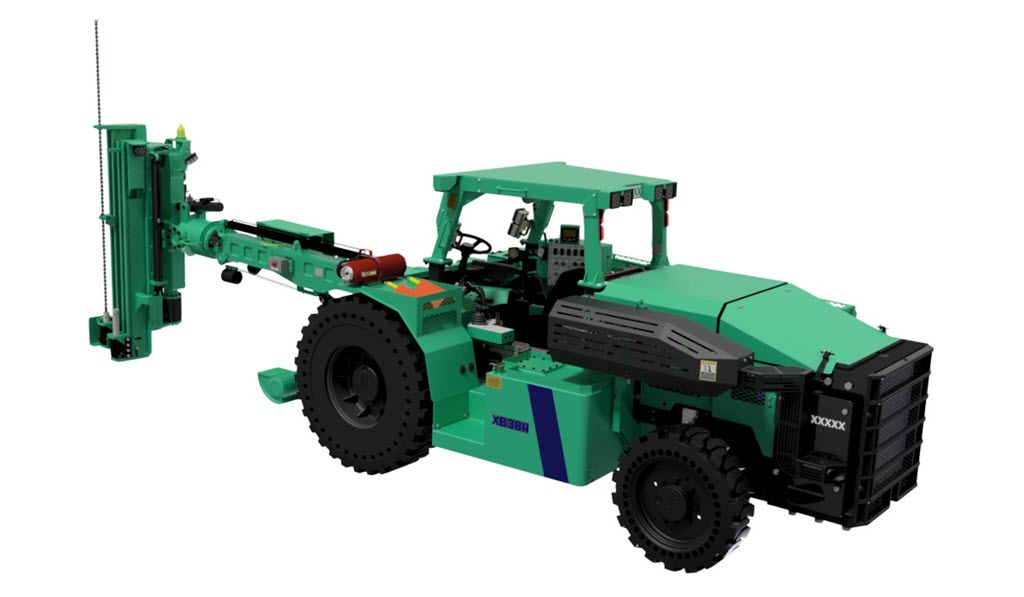
Series | Standard |
---|---|
Ground Clearance | 12 in |
Ground Clearance | 30 cm |
Turning Radius | 20 ft |
Turning Radius | 6 m |
Maximum Tramming Speed | 12 miles/hr |
Maximum Tramming Speed | 19 km/hr |
Tire Type | Solid Rubber |
Engine Type | QSF 3.8L Tier 4 101 hp |
Engine Type | QSF 3.8L Tier 4 75 kW |
Transmission | 4 Speed Powershift |
Tank Capacity | 65 gal |
Tank Capacity | 245 L |
Electrical System | 12-VDC 2,000 CA Starting Current Lockable Master Disconnect |
Electro-Hydraulic Control | Communication via Canbus Fieldbus |
Operating Hydraulic Pressure | 3,000 psi |
Operating Hydraulic Pressure | 20,685 kpa |
Maximum Bolt Length | 8 ft |
Maximum Bolt Length | 2.50 m |
Indexing Mast | Standard |
Fire Suppression System | Integrated Ansul Fire Suppression System |
Chassis Counterweight | Integrated Frame Counterweights Optional 1,000 lbs |
Chassis Counterweight | Integrated Frame Counterweights Optional 454 kg |
BELT STORAGE MAGAZINE
The easy-to-install Belt Storage Magazine (BSM) streamlines the conveyor belt requirements of a mine site.
Operating with multiple hydraulic and pulley systems, the Belt Storage Magazine maintains proper conveyor belt tension during dynamic start up, during normal operation, and even during a loss of power.
Engineered to store between 120 and 1,200 feet of conveyor belt and designed with both roof and floor mounting options, Prairie Machine’s Belt Storage Magazine is purpose built to meet the needs of any individual mining operation.
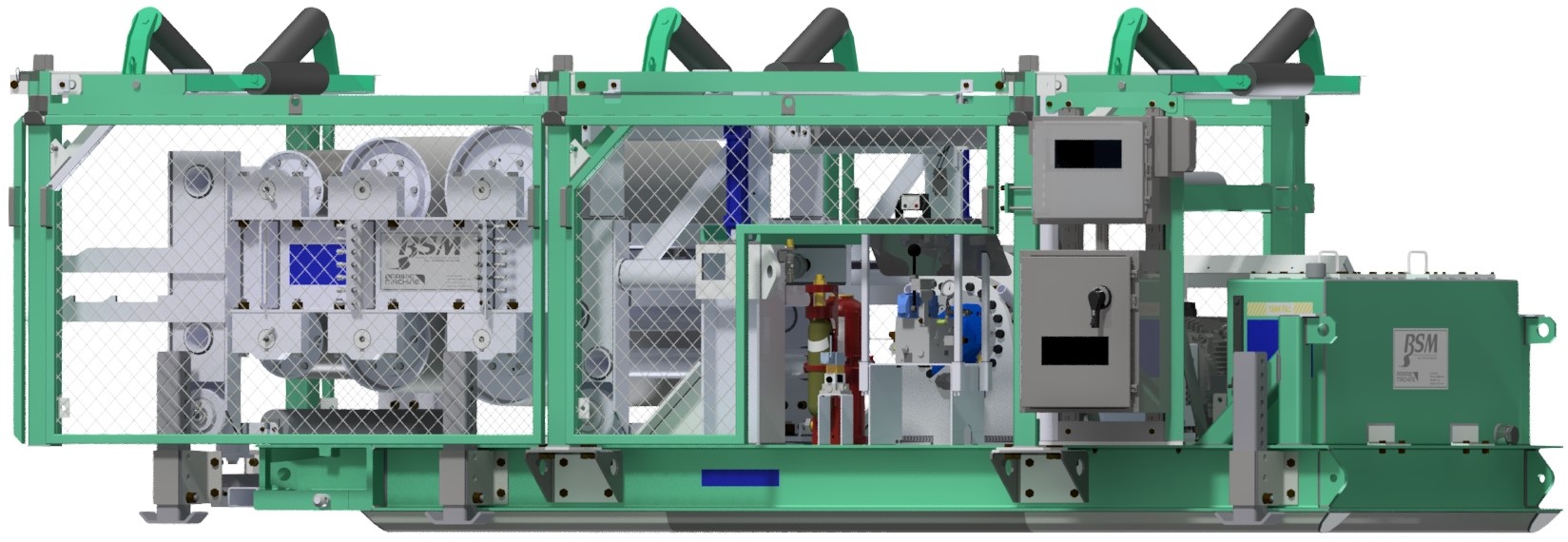
Series | Standard | High-Tension |
---|---|---|
Belt Take-Up Capacity | 120 to 1,200 ft | 680 ft |
Belt Take-Up Capacity | 36 to 365 m | 207 m |
Maximum Belt Reel-In Speed | 480 ft/min | 650 ft/min |
Maximum Belt Reel-In Speed | 146 m/min | 198 m/min |
Maximum Cable Reel-In Speed | 80 ft/min | 108 ft/min |
Maximum Cable Reel-In Speed | 24 m/min | 33 m/min |
Maximum Belt Reel-In Speed | 480 ft/min | 650 ft/min |
Maximum Belt Reel-In Speed | 146 m/min | 198 m/min |
Maximum Rope Pull Force | 24,500 lbf | 60,000 lbf |
Maximum Rope Pull Force | 109 kN | 267 kN |
Maximum Cluster Speed | 40 ft/min | 54 ft/min |
Maximum Cluster Speed | 12 m/min | 16.50 m/min |
Conveyor Belt Width | 3 to 5 ft | 3 to 5 ft |
Conveyor Belt Width | 1 to 1.50 m | 1 to 1.50 m |
Running Conveyor Belt Clearance | 18 in Wider than Conveyor Belt | 18 in Wider than Conveyor Belt |
Running Conveyor Belt Clearance | 45 cm Wider than Conveyor Belt | 45 cm Wider than Conveyor Belt |
Maximum T2 Belt Tension | 4,125 lbs (30,000 x 2/12 Strands) |
10,000 lbs (60,000 x 2/12 Strands) |
Maximum T2 Belt Tension | 1870 kg (30,000 x 2/12 Strands) |
4536 kg (60,000 x 2/12 Strands) |
Electric Motor | 75 hp 365 TC Frame 3-Phase 60 Hz Nema B Design |
150 hp 365 TC Frame 3-Phase 60 Hz Nema B Design |
Electric Motor | 56 kW 365 TC Frame 3-Phase 60 Hz Nema B Design |
112 kW 365 TC Frame 3-Phase 60 Hz Nema B Design |
Hydraulic Package | Integrated Into Frame or Remotely Mounted |
Integrated Into Frame or Remotely Mounted |
Mounting Method | Roof or Floor-Mounted | Roof or Floor-Mounted |
BELT CONVEYANCE EQUIPMENT
Prairie Machine's line of Belt Conveyance Equipment streamlines the conveyor belt system of any mine site. This diverse line of equipment is engineered to integrate into any mining operation and is utilized in everything from mine development to large-scale production.
All Belt Conveyance Equipment can be incorporated into any Prairie Machine Continuous Boring, Continuous Haulage, or Auxiliary Equipment system and can be custom-engineered to integrate into an already-established mining operation.
AUTO-DEPLOY CONVEYOR SYSTEM STRUCTURE
The Auto-Deploy Conveyor System Structure ensures that a conveyor belt line is stable and consistent.
The Auto-Deploy Conveyor System Structure is engineered for efficiency. Rather than handling them individually, operators load a sled of twelve conveyor stands onto the Auto-Deploy Conveyor Structure System. After securing just one conveyor stand, the remaining stands intermittently deploy behind an Xcel Continuous Boring Machine or tractor at a steady rate.
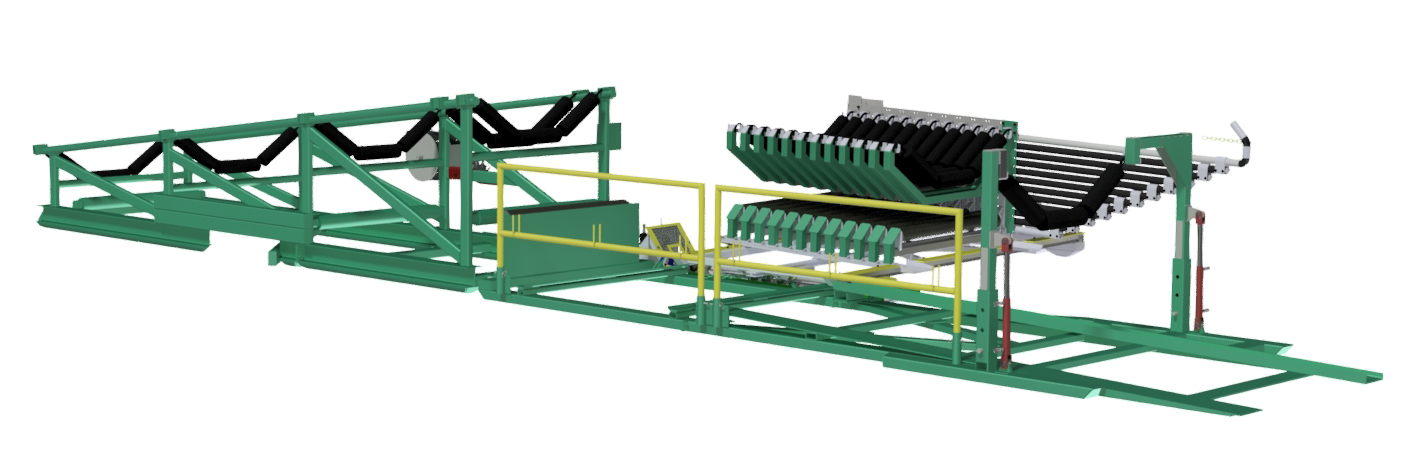
Series | Standard |
---|---|
Stands per Cassette | 12 |
Total Length of Deployed Structure | 81 ft |
Total Length of Deployed Structure | 25 m |
Space Between Deployed Stands | 6.75 ft |
Space Between Deployed Stands | 2 m |
Conveyor Belt Width | 2 ft |
Conveyor Belt Width | 60 cm |
Hydraulic System | External Supply 2,000 psi |
Hydraulic System | External Supply 13,790 kpa |
ANGLE STATION
Using just one conveyor belt, the Angle Station performs the job of multiple conveyor belt structures.
The Angle Station is designed to easily and effectively convey ore around a 90⁰ corner. The compact profile makes installing and relocating the Angle Station a simple task. Once in place, the Angle Station functions automatically without requiring a dedicated operator.
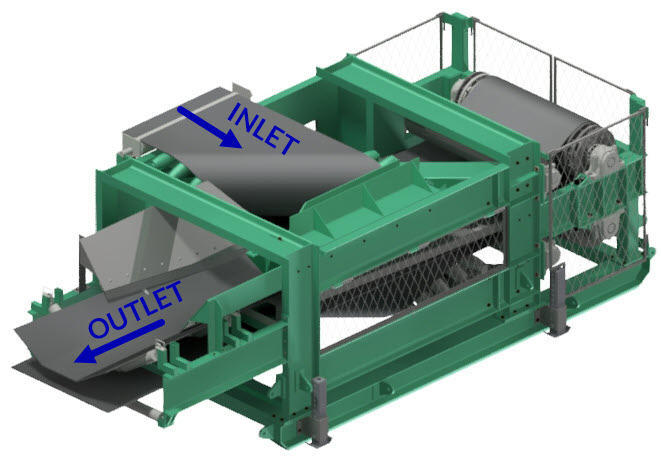
Series | Standard |
---|---|
Maximum Conveyor Belt Width | 48 inch |
Maximum Conveyor Belt Width | 122 cm |
Length | 20 ft |
Length | 6 m |
Width | 9 ft |
Width | 2.75 m |
Height | 7 ft |
Height | 2 m |
BELT STRUCTURE INSTALLATION CART
The Belt Structure Installation cart is a combination of Prairie Machine Flexiveyor Continuous Haulage technology and Rokion Battery technology. The Belt Structure Installation Cart provides a safe working space for assembling belt structure while the belt is in operation.
The battery powered Installation Cart straddles the floor conveyor with ample room to tram and maneuver. As the cart drives forward, it raises the conveyor’s ore side belt above a worktable, allowing for the installation of new belt structure. The belt naturally settles onto the new structure as the cart trams forward.
As Safety is always our priority, we keep the operator safe by using wireless remote control so the operator can run the machine from a safe distance. Furthermore, while stationery and personnel working in close proximity to the conveyor, specially designed guarding protects the operator from the running conveyor belt.
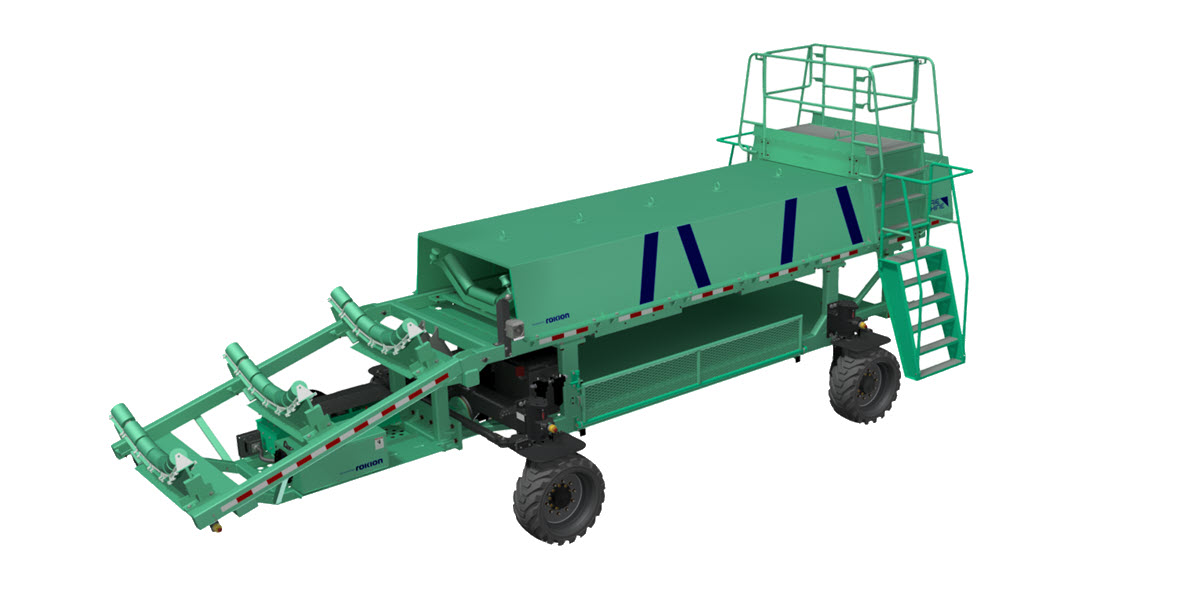
Type | With Crossover | Without Crossover |
---|---|---|
Height | 13'3" | 9'11" |
Height | 4 m | 3 m |
Width | 11'8" | 11'8" |
Width | 3.5 m | 3.5 m |
Length | 34' | 34' |
Length | 10.4 m | 10.4 m |
Wheelbase | 14'8" | 14'8" |
Wheelbase | 4.5 m | 4.5 m |
Tram High | 1mph (90ft/min) | 1mph (90ft/min) |
Tram High | 1.6 km/hr | 1.6 km/hr |
Tram Low | 0.5mph (45ft/min) | 0.5mph (45ft/min) |
Tram Low | 0.8 km/hr | 0.8 km/hr |
Weight | 23,400 lbs | 22,800 lbs |
Weight | 10,614 kg | 10,345 kg |
BELT WINDER
The Belt Winder safely and efficiently removes and reinstalls any size of conveyor belt.
The Belt Winder has multiple mounting options and is available in four standard configurations designed to suit the needs of overland, open pit, and underground environments.
- The compact Belt Winder 0110 can be easily moved from one location to another.
- The low-maintenance Belt Winder 0805 comes equipped with an onboard power supply for use in remote locations.
- The Belt Winder 0612 can retract up to 135 meters (450 feet) of conveyor belt at a rate three times as fast as the 0110 and 0850 models.
- The heavy-duty Belt Winder 0796’s rotatable spool frame and onboard belt clamp simplify any conveyor repair and maintenance processes.
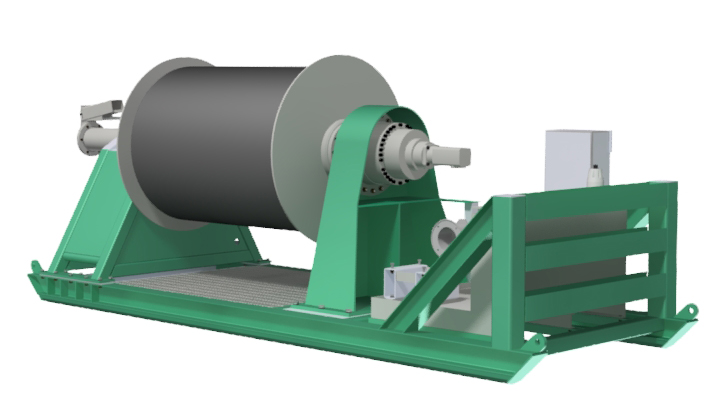
Series | 0110 | 0805 | 0612 | 0796 |
---|---|---|---|---|
Winding Speed | 5 rpm | 5 rpm | 5 rpm | 5 rpm |
Maximum Roll Length* (Based on a Conveyor Belt 5.80 in Thick) |
400 ft | 400 ft | 450 ft | 400 ft |
Maximum Roll Length* (Based on a Conveyor Belt 14.75 cm Thick) |
120 m | 120 m | 135 m | 120 m |
Conveyor Belt Width | 3.50 to 5 ft | 3.50 to 5 ft | 3.50 to 5 ft | 3.50 to 5 ft |
Conveyor Belt Width | 1 to 1.60 m | 1 to 1.60 m | 1 to 1.60 m | 1 to 1.60 m |
Installed Power Output | Externally Powered | 30 hp | 75 hp | Externally Powered |
Installed Power Output | Externally Powered | 22 kW | 56 kW | Externally Powered |
FEEDER BREAKER
The Feeder Breaker establishes a consistent flow of ore during haulage.
The Feeder Breaker accepts large, uneven pieces of ore from an Xcel Continuous Boring Miner or from any other mining machine. The Feeder Breaker's onboard conveyor system then moves the large ore through its cutting components and transfers the smaller, uniform ore to a Flexiveyor or to a mine site's extensible conveyor belt.
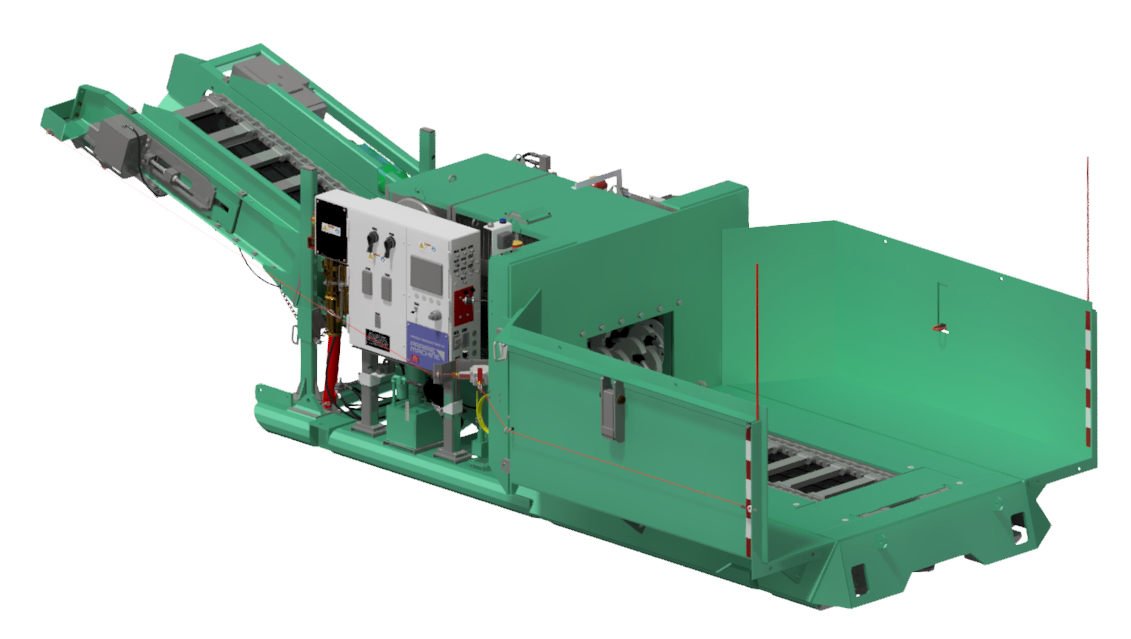
Series | Standard |
---|---|
Hopper Capacity | 6 yd³ |
Hopper Capacity | 4.50 m³ |
Breaker Shaft Speed | 65 rpm |
Peak Breaker Shaft Power Output | 147 hp |
Peak Breaker Shaft Power Output | 75 kW |
Breaker Shaft Pick Diameter | 24 in |
Breaker Shaft Pick Diameter | 61 cm |
Conveyor Speed | 61 ft/min |
Conveyor Speed | 18.50 m/min |
Conveyor Width | 29.50 in |
Conveyor Width | 75 cm |
Conveyor Power Output | 30 hp |
Conveyor Power Output | 22 kW |
Transport Height | 9 ft |
Transport Height | 2.75 m |
Discharge Height | 4.50 to 9 ft |
Discharge Height | 1.50 to 2.75 m |
Width | 11 ft |
Width | 3.50 m |
Length | 28.75 ft |
Length | 8.75 m |
SAFETY
Prairie Machine's line of Auxiliary Equipment is engineered with safety as its primary concern.
Integrated debris guards shield surrounding personnel and any adjacent equipment from the Auxiliary Equipment's moving components and from any ore that would have otherwise been lost during production.
The Fire Suppression System combats any overheating caused by the hydraulic components of the Xcel Roof Bolter, BSM, Belt Winder, and Feeder Breaker.