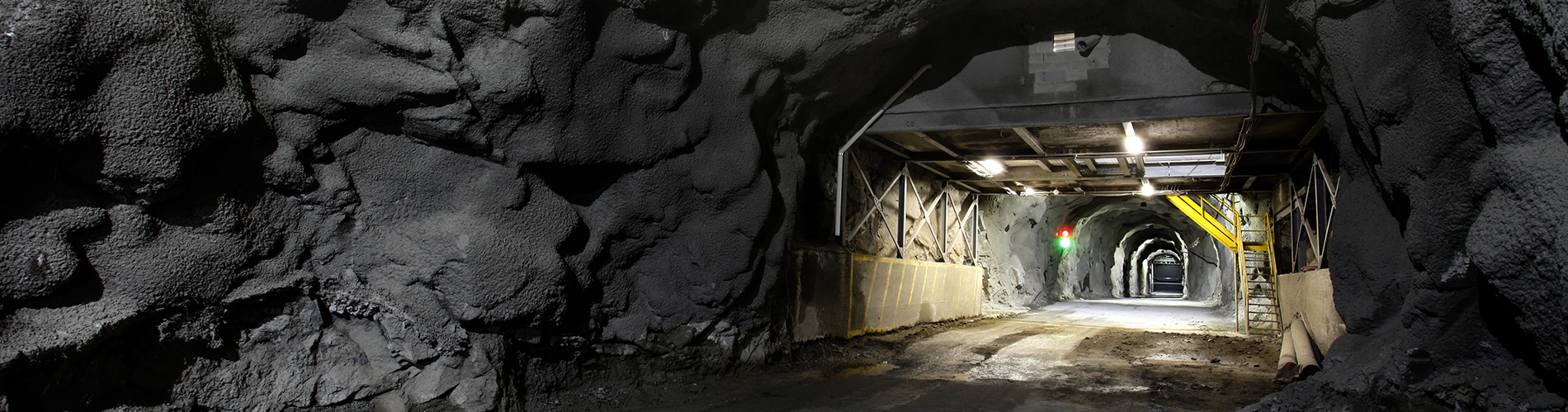
Posted March 3rd, 2025
Soft Rock vs Hard Rock Mining
The underground mining industry is vast and involves a variety of production methods, specialized equipment, and extracted products. Two underground mining categories are soft rock and hard rock:
For an OEM, the important differences between these mining practices are the methods for accessing the mine, the methods of extracting ore, and the safety risks present while at the mine site.
Accessing the Mine
In potash production mines, work crews are lowered from surface to the mine floor in an industrial elevator (or “cage”) and, once underground, are transported to their respective work sites. The equipment used underground is similarly lowered down to the mine floor and remains there until the end of its service life. A typical potash mine has relatively even terrain and a consistent ambient temperature of ~30°C. As such, trucks like the Standard Rokion R100 and R200 typically lack ramp preparation software and climate control options and feature open truck cabs.
In a hard rock mine, the work crew typically descends an access ramp to reach the mining floor. These access ramps range in length but can exceed 4 kilometers. Trucks like the Ramp Specification R200 and R400 are equipped with custom ramp preparation software to ensure that regenerative braking is available while ascending and descending a ramp, and while driving around the mine floor. Unlike trucks in a potash mine, hard rock mining trucks must be able to withstand the ambient temperature above ground, which fluctuates year-round, and underground, which typically exceeds ~30°C. To handle these extreme temperature changes, ramp trucks are outfitted with internal heating and cooling and typically feature a fully enclosed cab.
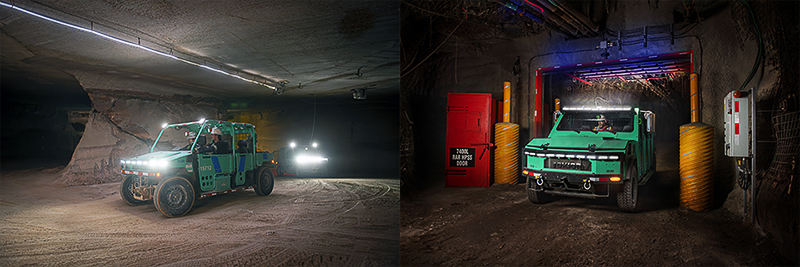
A Standard R100 in the Nutrien Cory potash mine and a Ramp Specification R400 in the Vale Creighton nickel, copper, and PGE mine.
Extracting Ore
The methods of extraction and the equipment used during this process differ depending on the product being extracted and the geological characteristics of the mine. Soft rock mines like Compass Minerals’ Goderich Salt Mine or Nutrien’s Cory Potash Mine may utilize continuous boring miners and a room and pillar mining technique. This process involves machine operators using a boring miner to mine seams of ore in a grid pattern, leaving large pillars intact to support the material overhead. The mining machine deposits ore onto a conveyor belt or continuous haulage system to remove it from the mine.
Hard rock mines like Vale’s Creighton Mine or Torex’s Media Minera Luna Gold Mine often use a drill-and-blast method of extracting ore. During drill-and-blast mining, operators use large drill rigs to bore a series of holes into the mine face. From there, workers carefully place explosives in the bored holes and detonate them to collapse the section of rock. After the section of rock has collapsed, workers remove the debris and repeat the process, as necessary.
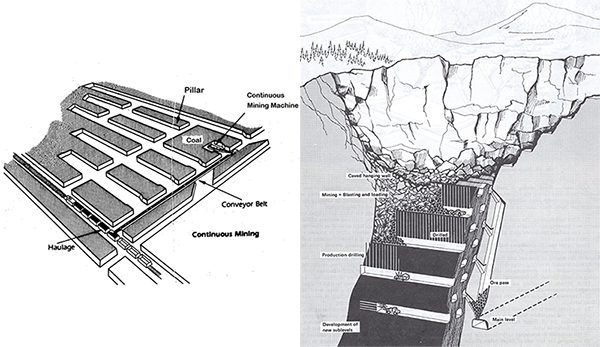
Examples of a typical room and pillar (left) and drill-and-blast (right) mining operation. Images courtesy of Energy Information Administration and Atlas Copco
Assessing the Risks
The underground environment, regardless of type, carries inherent risks for mine workers. Exposure to dust, heat, and poor air quality are among the dangers present in nearly every underground mine. In addition to these hazards, soft rock and hard rock mines present risks based on their different geological compositions and methods or extracting ore.
Methane gas exposure is a particular risk for coal miners. Methane gas is generated during the coalification process (the process in which organic material slowly converts into coal) and is released into the air when extracting coal from the mine. When the gas mixes with the surrounding air, the work area becomes vulnerable to explosions. To combat the risks associated with methane exposure, mines utilize underground ventilation systems and equipment manufacturers design special explosion-proof machinery and methane monitoring systems.
The drill-and-blast process utilized in some nickel and gold mines carry a unique set of risks to mine workers. The blasting process leaves the mine vulnerable to cave-in, falling rocks, and rock burst. Hard rock mines employ numerous methods of ground support, including roof bolting, mesh installation, and concrete reinforcement, to minimize these risks. To further protect work crews from the risks found in a hard rock mine, trucks like the Ramp Specification R200 and R400 have an optional Level II Falling Object Protective Structure (FOPS).
Purpose-Built Equipment
Among the many differences between soft rock and hard rock mining are the unique methods of accessing the mine floor and extracting the ore, and the variety of safety hazards present during each step of the mining process. Understanding the key differences between soft rock and hard rock mining is critical in designing efficient, effective, and, most importantly, safe mining equipment.